Case Study
Manufacturer Boosts Capacity Use and Revenues 15% – 20%
CLA helped a busy manufacturer connect disparate sources of data, leading to a 15% – 20% capacity increase and improved morale.
Share
Manufacturing
Organization
Manufacturer of consumer and commercial products used in the transportation industry.
Need
Evaluate and reorganize workflows to reduce equipment downtime.
Outcome
Capacity use and revenues up 15% – 20%.
Manufacturing
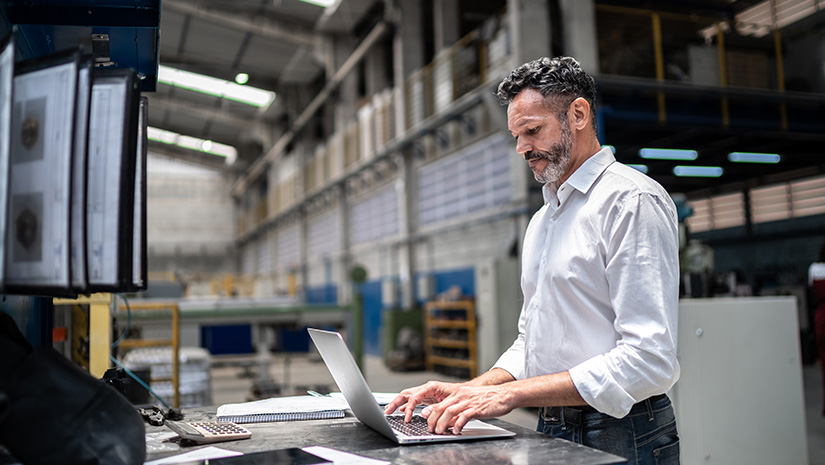
Organization
Manufacturer of consumer and commercial products used in the transportation industry.
Need
Evaluate and reorganize workflows to reduce equipment downtime.
Outcome
Capacity use and revenues up 15% – 20%.
Understanding the situation
A busy consumer product manufacturer was experiencing equipment downtime due to variability in production quality and yields. With approximately 100+ high-demand products running on 20 production lines, 24/7, each hour of downtime significantly reduced margins and profitability.
Shift by shift, management observed different productivity levels — and could not explain why. People were operating in silos based only on what they could see, rather than understanding the impact on other lines and staff. A culture of “we do what we’ve always done” restricted continuous improvement.
While one person’s priority might not be shared by others, a general lack of awareness around interdependencies resulted in significant inefficiency.
Exploring the challenge
The company turned to CLA for help. After analyzing their current state, CLA and management recognized additional capacity to reduce waste and significantly increase production flow throughout.
A team of top staff in production, maintenance, and information technology assembled to focus on yield, productivity, and downtime. Their approach involved combining technology with Lean Six Sigma to reorganize workflows and measure the impact of making changes.
CLA used artificial intelligence (AI) to process the vast amounts of digital information coming from the different production lines. Equipment was installed on machines to feed real-time data into informative, convenient dashboards. Computer vision cameras were added to perform final quality inspections.
Change management and training were key to success, championed by senior leadership. The new approach captures the effectiveness of corrective actions. It’s now about quantity and quality of each fix.
Achieving results
In the past, volumes of spreadsheets needed to be compiled and analyzed to figure out problems and attempt fixes. Using data and AI to connect siloed data sources and analyze workflows enabled a “get-it-right-the-first-time” shift, which had a huge impact on morale throughout the company.
The company’s capacity utilization and revenues improved by 15% – 20%, and no new production lines, capital investment, or staff were required. It’s no longer about what one person can do alone, it’s about the impact and interconnectedness of the entire team on the shop floor and their new perspective on continuous improvement.
CLA helped put the company in a prime position to scale up for growth without a capital outlay or additional staff.